1834
Birth in Peterhead, Aberdeenshire of George Kynoch.
ca
1856 Kynoch joins Pursall and Phillips of Whittall
Street in central Birmingham, manufacturers of percussion
caps.
1859
Catastrophic explosion at the company on September 27th,
killing 19 of its 70 employees including children, gravely
injuring many others, devastating the factory and damaging
the surrounding area.
1861
Mr Pursall applies for and is granted permission to build
a powder magazine and percussion cap manufactory on a
4 acre site at Witton, a country hamlet in a safer location.
1862
George Kynoch is formally recognised as proprietor. An
old shed is trundled on rollers to Witton from
the city factory, linked to a new and bigger one (right)
and operations start with a staff of one man and 12
girls. This is at a time when significant developments
are being made in ammunition technology and especially
the development of the Boxer cartridge which comprises
a case made of thin coils of brass held together with
paper and a brass cap chamber.
1867
Growth has been huge for Kynoch & Co. at the Lion
Works, as it is now called. (The factory in this
year below).
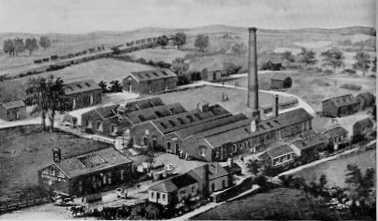
1870s
George Kynoch makes several significant advances
in cartridge development which are protected by patent.
1870
Whilst the safety record in percussion cap manufacturing,
run by the redoubtable Mrs. McNab, is excellent, that
of cartridge manufacture is not. The fourth explosion
at the factory in two years is reported, this one on November
17th killing eight and injuring twenty, including children.
On December 9th an even more appalling accident occurs
in the neighbouring cartridge factory of Ludlow &
Co - possibly a Kynoch licensee - when 17 people are killed
instantly and 34 more will die later from their injuries;
a national outcry ensues.
1872
George Kynoch purchases a further 19 acres of land.
1877
A rolling mill is leased in Water Street, Birmingham.
1882
By this time, after just twenty years, George Kynoch owns
the second largest ammunition factory in Great Britain
on a site of 24 acres, a brass rolling mill elsewhere
in Birmingham, a patent lamp business, and a printing
office. Daily cartridge capacity is now 400,000 and there
are 800 employees.
He is about to buy a gun factory and he has even
bigger plans for the Lion Works factory and also for political
and public service - requiring more money and more personal
time.
1884
A memorandum of agreement between George Kynoch Esq. and
G. Kynoch & Co. is drawn up by which George's interests
are effectively bought out. A Board of Directors is appointed
and George Kynoch will be Managing Director.
1886
The new structure is not proving a success. The Company
is in serious decline. George Kynoch is elected Conservative
Member of Parliament for Aston.
1887
Relations between George Kynoch and the Board are at breaking
point. Within the factory quality standards have dropped
with a corresponding effect on costs and the health of
the business as a whole.
1888
The disputes between George Kynoch and the Board come
to a head and he is forced to resign. Arthur Chamberlain
joins the Board and is appointed Chairman. He will serve
for the next 25 years.
1888/9
Two unsuccessful Kynoch enterprises are disposed of, the
lamp factory and the gun business. The metal rolling plant
in
Water Street, owned by George Kynoch, is bought by the
Company and an option to purchase is obtained on a larger
mill in Lodge Road (left). These moves give
the Company security of metal supply and control over
quality. Work is started on a new .303 plant, a Q.F. (quick-firing
shell) factory and a fuse-making department. Determined
measures are taken to improve quality control. 85 acres
of extra land at Witton and Streetly are obtained in order
to provide improved magazines and adequate proof ranges.
Attempts to change the factory name from Lion Works -
too closely associated with George Kynoch - to Witton
Ammunition Works are however unsuccessful.
1891
George Kynoch dies in self-imposed exile in South Africa.
Meticulous attention to quality within the factory is
bringing its own reward in the form of additional Government
contracts.
The
Company is complimented by H.M. Chief Inspector of Explosives
on its safety arrangements. In addition to its military
ammunition work the Company is producing half a million
sporting cartridges a week. Annie Oakley, on tour with
Buffalo Bill, pays tribute to them.
The
Water Street mill is closed and production concentrated
at the developing Lodge Road factory; a cupro-nickel casting
shop is built at Witton; and a part-time consulting metallurgist
is appointed.
A serious dispute halts production and all 3000 employees
join the strike which has started over the alleged malpractice
of a foreman in using apprentices to do the work of skilled
toolmakers. Despite this the Company is generally recognised
as one which pays well and treats its employees in an
enlightened manner.
1893-1896
Kynochs enter the field of high explosive production by
purchasing a Yorkshire company, Shortridge & Wright.
A new factory is built (1895) on a 170 acre site at Arklow
on the east coast of Ireland to produce cordite. Very
quickly gelignite, dynamite and Kynite will be
introduced to the range. And such is the success of this
venture that a second factory is soon planned, this time
on a 750 acre site in Essex, christened "Kynochtown".
Glycerine will also be produced at the Lion Works, together
with soap and candles (7- 8 tons of them per week) made
from the by-products of glycerine manufacture.
A
Siemens-Martin steel melting plant is installed at Witton
to supply Birmingham manufacturers with a variety of steel
castings and to permit the manufacture of shells of various
types including armour-piercing. A new Bullet Shop is
created. Witton's first rolling mill is laid down together
with a casting shop. Its purpose is to satisfy Lion Works's
need for the brass required for ammunition production,
leaving the Lodge Road factory to concentrate on trade
with third parties. The Company is rolling 100 tons of
brass a week. There are also plans for setting up plant
to make bicycle components. The Machine Shop is shown
right.
1897
The shareholders are warned that the Company will need
to raise further capital to finance this rapid rate of
development. They willingly comply and a new company is
formed, Kynoch Ltd. with a nominal capital of £500,000
and with Chamberlain still its chairman.
1897-1898
A period of further rapid development. At Witton the new
bicycle plant is producing 200 sets of components (hubs,
pedals and brackets) each week. Large additions are made
to the ammunition plants. Lion Works is for the first
time equipped to cast and roll all of its cartridge brass.
Production of candles reaches 60 tons a week. A Kynoch
machine gun is introduced.
The
Company's fleet, comprising the Anglesey and the
Kynoch ship explosives from the Arklow factory
to England. The Essex factory, Kynochtown, has grown to
large proportions and incorporates a Company village:
a new company, Kynoch Estates Co. Ltd., is formed to administer
it.
1899
The Arklow plant is brought to a standstill because
Anglesey is marooned behind a wall of silt. This
prompts the purchase of a dredger.
Shortage
of work leads to temporary shut-downs at Witton of the
Cycle Department and brass casting workshop, followed
by general short-time working except for the steel, shell,
soap and glycerine departments. Outside powder suppliers
object to the increasing use by Kynoch of its own smokeless
powders in cartridge production on the grounds of unfair
competition. Kynoch's response is brutal: henceforth
it will only accept orders from its own customers which
specify use of Kynoch powder.
The
Kynoch Journal is inaugurated - a serious technical
journal produced by the Kynoch Press which has at the
same time been printing "the scores of millions of sporting
cartridges sold".
The outbreak of war in the Transvaal transforms the Company's
position and leads to heavy demand for most of its products.
1901-1902
Kynoch acquires various new businesses and premises: the
Eyre Street factory of
Hadley
& Shorthouse, producing nails and brass and copper
tubes and wire; a large factory at Stirchley to produce
armour-piercing and shrapnel shells; Forward Engineering
Company which adds gas engines (left) to
the existing engineering portfolio of machine guns and
roller bearings; a paper mill in Ireland; and perhaps
most significant of all Accles Limited of Holford Works,
a run-down ammunition company on an adjoining 33 acre
site.
1904
A new office block is opened at Witton (right).
1906
A second Irish paper mill is purchased. Negotiations start
on the purchase of a South African explosives factory.
A project is launched to establish "a pleasure resort"
on Canvey Island complete with pier and promenade.
New
plant to make soap is installed at Witton and at Eyre
Street to make tintacks. The metric system is introduced
into the nine Company factories, not wholly successful
as the Chairman is 70 years ahead of his time. A more
successful initiative is the establishment of the Research
Laboratories (right)
comprising two large rooms and two small ones launched
with confident expectation of success: "....it is certain
that the Kynoch Metallurgical Laboratory, with its motto
of 'Thoroughness', has a brilliant future".
1907-1910
The trading results for the 1906 financial year show a
big deterioration and those for 1907 reveal an 80% fall
in profits from their normal level. No dividend is declared.
A debenture stock issue is under-subscribed and the Company
is forced into drastic cost cutting measures, including
the dismissal of staff. This decline in the Company's
affairs is due to the rise in material costs and a reduction
in Government orders, due partly to the "cordite scandal"
whereby a rejection by the Government of a large consignment
of cordite leads the Company to take legal action against
its customer. Relationships are soured. The Government
refuses to do business with the Arklow plant, now disposed
of and renamed Irish Manufacturers Ltd. in an attempt
to blur the link with Kynoch, and the new company quickly
fails. Cost cutting continues up until 1910: there are
protracted shutdowns at Witton and elsewhere. The Endurance
Works at Stirchley is sold off and the Company's convalescent
home at Llandudno is disposed of.
Despite its large size the new explosives plant in South
Africa, built to provide all the Transvaal goldmining
groups, cannot cope with the demand and needs extension.
1912
Things are looking better. The turnaround is across all
departments. There is a short-lived revival in interest
in motorcycle manufacture.
1913 Arthur Chamberlain dies
after 25 years of service. He is succeeded by his son,
Arthur Chamberlain Junior. The new chairman quickly disposes
of the two paper mills and decides to give more attention
to metal production. The casting and rolling shops have
had long periods of idleness and have in fact not operated
since the beginning of 1913. Nevertheless they are restarted
and additional rolling plant is installed.
1914-1918
Within weeks of the outbreak of war the Company contracts
to make an additional 3 million cartridges a week and
progressively increase the weekly output to 7.5 million.
As time goes on huge contracts follow for shell cases,
detonators, cordite, acetone and other products . At the
peak of the war effort 18,000 people are working at Witton.
Their typical weekly output will be:
- 25 million rounds of rifle ammunition
- 700,000 rounds of revolver ammunition
- 5 million cartridge clips
- 110,000 cartridge cases for field guns.
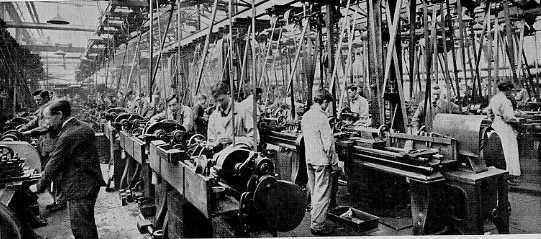
Many of these 18,000 are women, known locally as "Kynoch's
Angels".
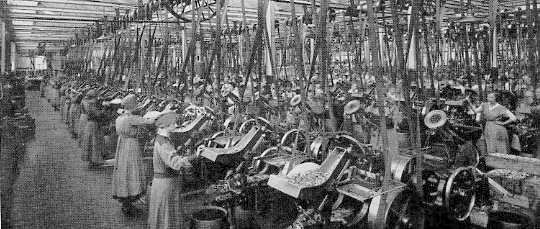
Pay
is good for all. Protection is given by the Company to
employees serving in the forces.
H.M.
King George V visits Witton on July 23rd 1915.
By the war's end 3.5 billion small arms cartridges will
have been produced and there will be a weekly cordite
output of 200 tons, a ten-fold increase over the previous
level. The Company has to look forward to a post-war period
when demand for these products will fall drastically and
national capacity will far exceed the business available.
The future is one of unavoidable rationalisation, an "explosives
merger".
In
November 1918 a new company is born, initially named Explosive
Trades Ltd. but quickly changed to Nobel Industries. This
is a merger of Britain's explosives interests centred
on the biggest manufacturer, Nobel Explosives. Kynoch
Ltd. is a part of this and finds itself sharing an uncomfortable
bed with its former competitors in the fields of explosives
(Nobel and Curtis & Harvey), ammunition (Eley) and
metal processing (locally, Kings Norton Metal Co. which
possesses facilities for brass and copper strip rolling
and rod extrusion as well as interests in coin minting
and ammunition; and Birmingham Metals and Munitions Co.
manufacturing rolled copper and brass and solid-drawn
brass cartridge cases). These two companies and Kynoch
Ltd. represent "the Birmingham end" of Nobel's interests
and are managed by "The Birmingham Committee" chaired
by Arthur Chamberlain and his deputy Sir Harry McGowan.
1919-1920
Rationalisation is drastic and painful. Kynochtown and
Kynoch-Arklow disappear. The facilities for rolling at
Lodge Road and Eyre Street are sold off. Birmingham Metals
and Munitions is put into liquidation, with Kynoch taking
over part of its Adderly Road site. Extra investment is
put into the Witton and Kings Norton mills. Facilities
are installed to produce zinc strip as are five electric
furnaces for melting brass - a significant pioneering
step. Two chain machines are installed and five staff
transferred from other duties to start making an interesting
novelty invented in the U.S.A., the zip fastener. There
is also investment in creating reliable outlets for existing
products especially in the promising aircraft and motor
sectors: holdings are acquired in John Marston Ltd., Wolverhampton
(motorcycles, radiators and radiator tubes), Amac Ltd.
of Aston (motorcycle carburettors) and Excelsior Motor
Radiator Co. Ltd. of Leeds (aircraft radiators). With
the disappearance of its huge explosives and military
ammunition business as well as its carefully cultivated
image of an influential and distinctive concern, Kynoch
Ltd. has changed almost beyond recognition.
1920-1923
Many new products are
tried: motor lamps, oil heaters, lanterns,
padlocks, mincers, textile bobbins and cycle pumps from
compressed paper, two-speed gears, petrol pumps, and home
safes, none of which will be successful. Glycerine production
is transferred elsewhere in the Nobel Industries organisation
and the cycle, soap, candle, gas engine and engineering
departments are at a standstill due to the general depression.
But the company perseveres despite apathy and suspicion
with one new product, the zip fastener.
1922
Staff salaries are cut by 10%.
1923
Arthur Chamberlain resigns as chairman of the local Board
and is replaced by Sir Harry McGowan who is also Chairman
of Nobel Industries. The South African explosives interests
are transferred elsewhere in the Nobel Industries organisation
and the Witton activities of soap, candles, cycles and
general engineering products are abandoned. The site's
activities now comprise effectively "the ammunition side"
and "the metals side". Three departments at Kings Norton,
especially involving strip, are re-opened to meet increasing
demand.
1924
Three more electric melting furnaces are ordered.
1925
Investment is made "to fit up the old Machine Shop at
Witton to undertake metallic work for sporting cartridges
and metal sundries". Copper consumption soon reaches 400
tons per month. Despite Eley being the senior partner
in the area of sporting ammunition within Nobel Industries,
Kynoch Ltd. succeed in persuading the Nobel Board to concentrate
all production on the Witton site. The transfer of plant
and personnel from Eley's Waltham Abbey factory, and the
transformation of production facilities at Witton, will
be a long and gradual process. The Eley name is preserved
by renaming all Nobel sporting ammunition "Eley-Kynoch".
1926
A new company is formed: Lightning Fasteners Ltd., to
handle the zip fastener business. Significant investment
is made in sporting ammunition facilities and in the mills,
especially for rod extrusion. Lightning Fasteners now
has a French factory and is considering a German. Amac
is merging with two other motor accessory firms to form
Amalgamated Carburettors Ltd. (Amal).
In May the General Strike brings all industry to a standstill
for nine days.
In December there is a bombshell: the announcement of
a merger of Nobel Industries Ltd., Brunner Mond &
Co. Ltd., The United Alkali Co. Ltd. and British Dyestuffs
Corporation Ltd. The new, and huge, company will be called
Imperial Chemical Industries Ltd.
1927
Before the full impact of this merger hits Kynoch
Ltd. a far-reaching review is made by Management of metal
activities. Plans are laid for a £250,000 reconstruction
scheme: yet more money is invested in electric smelting,
a new factory for Lightning Fasteners is created on the
Witton site
(above)
and output of extruded rod reaches 3500 tons.
1928
The ICI Board decides that priority is to be given to
the development of the metal side of Kynoch's business.
Lion Works becomes the headquarters of the Metal Group
of Imperial Chemical Industries Ltd. Two further companies
join the Metal Group with Kynochs and King's Norton: Elliott's
Metal Co. Ltd. of Selly Oak (rolled brass and copper,
copper wire and tubes); and British Copper Manufacturers
of Swansea (copper refining and processing, wrought metal
products, also zinc refining and processing and fertiliser
and chemicals production, all at their premises at Landore).
1929
The name of Kynoch Ltd. disappears and is replaced by
ICI Metals Ltd. And the Lion Works becomes Kynoch Works.
Allen Everitt & Sons of Smethwick (non-ferrous tubes,
especially copper-nickel condenser tubes produced in a
state-of-the-art factory) also joins the Metals Group.
For the second year in succession the Company wins the
Senior TT race on the Isle of Man with a little help from
Marston's Charlie Dodson and his works "Sunbeam" motorcycle.
A Sunbeam is also second and Marston wins the team prize
for the third year in succession.
1930-1932
Rationalisation is again inevitable, especially in the
face of a deepening slump. King's Norton Metal Co. is
put into
voluntary
liquidation. The business of extrusions, coins and metal
sundries, and many personnel with it, are transferred
to Witton whilst the Metal Group continues to rent rolling
capacity there. All is not gloom despite the grim times
and particular success is found in the areas of .22 rimfire
ammunition, zinc battery tubes and zip fasteners.
The new Witton Strip Mill (right) is completed
and opened, for its time a truly revolutionary enterprise.
Many new schemes resulting from ICI's enlightened employment
policies are put into place.
1933
A worldwide survey on ammunition prospects lead to the
opening of a factory in Australia and the establishment
of a game research centre in Hampshire. The recently acquired company of Crown Copper Mills (a.k.a. Roberts) of Garston, a rolling mill established in 1880, is closed down.
1934
The Strip Mill is producing 500 tons a month and annual
Rod Mill capacity has soared to 14,000 tons. Broughton Copper Co. of Salford whose activities include a wide range of tube production, is purchased. Witton
research creates three new copper alloys: Everdur,
Kuprodur and Kumanal, perhaps the first
examples of the "new metals" which will emerge from the
site in the following years.
1935
Witton's own tube mill is commissioned.
1936
After much deliberation a decision is made to establish
a pilot scale aluminium plant at King's Norton with a
capacity of half a ton per week. A concerted sales drive
on the aircraft companies is made. Another Broughton company, John Bibby and Co. of Garston, a rolling mill established in 1865, is closed and production transferred to South Wales.
1936-1939
Throughout this period the lot of employees steadily improves.
"Privilege" Saturday morning leave is granted to staff
and foremen. Also "marriage is now no bar to employment
of women on the works payroll". A 1500-seater Oscott canteen
and a dental clinic are opened. Marston's "Sunbeam" motor
cycle business is sold (1937). The Board adopts a policy
(1937) of containing external sales of several products
"so as to clear the way for the Government's defence requirements".
The Witton Q.F. (quick firing) shell shop is completely
reconstructed. A "shadow factory" is erected on the Landore
site for the production of large calibre Q.F. shells.
Casting capacity is increased for extruded rod. The filling
of flame tracer bullets is mechanised. One shop is extended
to absorb the manufacture of steel cores for armour-piercing
bullets. Buildings at Holford are re-equipped to make
detonators. There is a complete modernisation and reorganisation
of metallic ammunition production (1938). The building
is sanctioned of a full scale aluminium production unit
in the Holford area. Many other measures are taken throughout
the Witton site to extend production and make it more
efficient and effective. Production support facilities
are substantially improved also, with renovated offices,
a modernisation of the Power House and the building of
a two-storey research block. New factories are built for
John Marston and for ammunition production in Eire and
South Africa, and new premises are found for Excelsior.
Confidential discussions occur between the Company and
the Government about future agency factories. In many
respects the associated companies within ICI's Metal Group,
and especially Kynoch Works, are by 1939 ready for war
which finally overtakes them and the country as a whole
on 3rd September 1939.
A few weeks later, on October 26th, King George VI visits
Witton
1939-1945
Thousands of extra personnel are absorbed, and by 1943
20,000
people
are working at Witton. Many perform duties additional
to their normal work, such as firewatching, Home Guard,
manning of first aid post or ambulance depot and membership
of the rescue team or the Red Cross detachment. Young
and old serve, women and men. For years, they devote one
or two whole nights a week, entirely voluntarily and without
pay, over and above their daytime duties. The level of
effort, especially after Dunkirk in June 1940, is exhausting.
From its eleven factories in 1939, the Company will by
1943 be running 27 factories on 20 separate sites employing
50,000 people. This increase occurs because of the Company's
need for extra capacity and also its responsibility for
managing Government agency factories with their 15,000
people.
The
Company is asked to design, build and operate a new aluminium
plant at Waunarlwydd in South Wales. By 1940 it has a
new radiator tube factory operational at King's Norton.
By 1941 the Ministry of Supply is building two new ammunition
factories at Hayes in Middlesex and Summerfield, near
Kidderminster; Metal Group will operate both of these.
Negotiations are going on to find additional production
capacity at John Waddington in Leeds and in several Kidderminster
carpet firms. In 1942 the Metal Group assumes responsibility
for another radiator tube factory at Burton. Steatite
and Porcelain Products of Stourport (ce
ramic
products) is acquired in 1941.
Numerous, often massive extensions are made to existing
facilities including no less than three extensions for
John Marston which in 1943 is merged with Excelsior to
become Marston Excelsior Ltd. Amal is moved into new premises
due to fire in December 1943.
The
range of different ammunition types produced at Witton
is vast, from small arms ammunition to large Q.F. cases,
from detonators to anti-tank devices. Throughout the group
67 different types of cartridge are produced. The war
work extends of course to all the metal activities and
Witton's copper and brass output peaks at 3000 tons per
week. Demand for aluminium is insatiable. Outside Witton,
Marston, Excelsior and several other factories are wholly
devoted to aircraft components. Marston's development
of non-metallic, self-sealing aircraft fuel tanks is especially
significant. Much of all this work is secret.
Even
more secret is the Metal Group's involvement in the "Tube
Alloys Project", Britain's atomic energy effort, especially
in connection with development of methods of separating
the isotope U235 from uranium and of new uranium fabrication
techniques.
Luftwaffe
bombing raids on Kynoch Works occur since it is of course
a large and prime target. Between 1940 and 1943, 47 high
explosive bombs fall on the site and more than four thousand
incendiaries. Surprisingly, these result in only two fatalities.
A memory of at least one attack will survive: the night
of 18/19th November 1940 when the Rod Mill is damaged
and the test house and the mill office are wrecked. There
are anti-aircraft defences in the neighbourhood which
guard the factory, including a battery in Perry Barr Park.
By
late 1944 ammunition production is running down, the Hayes
factory is scheduled to close, the carpet manufacturers
will shortly get their factories back and the countrywide
payroll falls to 33,000. Working hours have already reduced
to more acceptable levels from the earlier peaks, the
previous intensity of working and the lack of leisure
time having given Management from 1942 onwards increasing
concern over the risk to health and sanity. Redundancy
and resettlement schemes are in hand. In August 1945 a
flag flies over Kynoch Works in tribute to the hundreds
of employees still in the Services, the sixty-four who
will never return, the seventeen civilians nationally
honoured for their services to industry and the 15,000
employees still working on the site.
Shortly
afterwards the Metal Group is given a new title: ICI Metals
Division. The company named ICI Metals Ltd. ceases to
exist.
1946-1947
The slowing down of demand since 1944 has made the process
of adjustment less difficult. Sporting ammunition is rehabilitated.
The metal interests will benefit from huge demand as postwar
reconstruction gathers pace. Wrought aluminium is needed
for prefabricated housing and the Company takes over the
Waunarlwydd facility from the Government. Marston starts
to produce aluminium furniture and sinks, at the same
time developing its welding and brazing skills for this
material. The demand for tubes, for housing and marine
and power generation condensers soon outstrips the capacity
of Witton, Smethwick and Salford. Several expedients are
used to meet the demand across the product range: the
Ministry's King's Norton factory is used for zinc strip
manufacture and later as an overflow for plumbing fittings
and radiator tubes; in another unit there brass wire is
produced; the Swansea Q.F. factory becomes a Lightning
Fasteners offshoot. More permanent plans are laid: the
conversion of the Holford aluminium plant to copper sheet
and strip production; a major capacity increase in the
Rod Mill; and a large scheme to modernise the Witton Strip
Mill.
A
general shortage of labour is partly offset by the need
to absorb, via a careful resettlement programme, employees
returning from the Services: in one six month period 1000
people are re-introduced. The Division's payroll levels
out at about 17,000.
Welcome innovations are made in employees' conditions
of employment. After a year's trial a five day working
week is introduced and production shows a slight increase.
The Division's first training school for indentured apprentices
is opened. A near-hurricane damages several factory buildings.
The Broughton tube works is flooded. The harsh winter
of 1946/1947 brings an accelerating fuel crisis which
makes life a misery and eventually halts production.
1948
A minimum of two weeks paid holiday is introduced for
all employees. Only now does the postwar boom show signs
of waning. Major reconstruction plans are laid. Tube making
capacity needs to be extended and rationalised. Work begins
on the largest and best-equipped tube mill in the country
at Kirkby near Liverpool.
1948-1949
Amal moves into a new factory in Holdford Road. Another
47 acres is purchased at Waunarlwydd. ICI's new Creep
Test Research Centre is built at Witton. The Board votes
a modest sum for research into titanium and its alloys.
The
1950s
This is a decade of progress, innovation and rationalisation,
against
a
background of fluctuating market conditions. Production
starts in the new tube mill at Kirkby: the Witton mill
closes and Broughton will soon follow. Smethwick concentrates
on brass tubes. Extensions to Witton's strip, sheet and
rod mills are completed. The Kynoch Press is modernised.
Lightning Fasteners opens a new factory at Waunarlwydd.
The Company is engaged on secret development work on rocket
motor design at Summerfield. At Witton a new multi-storey
office block is built, "Beeching's Folly". A new instrument
workshop is created. The Power House and Telephone Exchange
are refurbished and the main office entrance area, apparently
untouched since 1904, is dramatically modernised.
The
decade sees the birth of the first of the "new metals",
the first new structural metal in Britain for half a century
(1955). After much research work at Witton and elsewhere
within ICI, the technology of melting titanium is established:
a melting plant is built at Witton and fabrication techniques
are developed at Kynoch Works and Marston Excelsior, opening
up opportunities in the nuclear engineering, chemical
plant and other industries. Three years later it is joined
by a second new metal, zirconium. Hafnium, niobium, vanadium
and, most demanding of all, beryllium which requires a
wholly new factory will all follow.
The
need for rationalisation in the tube industry becomes
apparent and Metals Division joins forces with a former
competitor, Yorkshire Copper Works,
and
forms Yorkshire Imperial Metals Ltd. (1958) which absorbs
the businesses at Kirkby, Smethwick, Carolina Port (Dundee)
and Landore. Similarly in the aluminium field the Division
cooperates with the Aluminium Company of America to form
Imperial Aluminium Company Ltd. - Impalco - which will
operate as a separate commercial venture (1959). Following
the visit to Witton in 1915 by King George V and that
of her husband King George VI during the Second World
War, Queen Elizabeth the Queen Mother tours the site in
May 1957.
Meanwhile
the Company's markets are fluctuating wildly. By 1952
the seller's market has gone, foreign competition is increasing
and business is slack. But by 1954 conditions "were never
more satisfactory" although this will not last; in 1958
the conditions are "strenuous, uncomfortable and often
discouraging".
The
1960s
A decade of increasing independence during which a strategy
of vertical integration and horizontal diversification
in the product range is adopted.
Text
© staffshomeguard.co.uk 2007-2019
Images ©
IMI plc 2002-2019v2.1 - 10th April 2008